关键技术或设计特征
采用重金属-氨氮-水的药剂强化热解络合-分子精馏分离技术,实现氨氮污染物削减率大于99%,同时全过程无废水、废气、废渣等二次污染产生。
资源回收率高,将废水中分离出的氨氮回收为高纯氨水,重金属回收为金属氢氧化物,可回用于生产工艺或直接出售。
通过专用塔内件设计技术实现传质效率提高,漏液降低,拓宽设备弹性负荷。
动态集成控制技术实现操作安全性,保证出水合格率为100%。
典型规模
原水氨氮浓度:1-70g/L;
原水重金属浓度:10-200mg/L;
处理规模:50-3000吨废水/天。
处理后水中氨氮浓度优于国家排放标准《中华人民共和国污水综合排放标准》(GB8978-1996)一级标准。
推广情况
在钒、钼、镍、三元电池、稀土、锆、铌钽等行业完成示范工程应用。
14、机械蒸汽再压缩污水处理技术
适用范围
城市污水,化工、制药、印染等行业废水处理
基本原理
该技术针对蒸发过程中的余热蒸汽进行循环利用,采用水蒸汽压缩机将蒸汽进一步压缩作为热源来循环加热浓污水使其蒸发,而压缩后的蒸汽冷凝为水一部分进入压缩机对其进行润滑密封,另一部分进入预热器对原液用于预热原液,实现余热蒸汽的全部回收利用。
工艺流程
工艺流程为:1、废水首先进入原料缓冲罐;2、原液从原料缓冲罐经进料泵泵入预热器预热后进入蒸发器蒸发;3、蒸发器中蒸发产生的二次蒸汽和未蒸发的原液一起进入分离器进行气液分离;4、二次蒸汽在二次分离器中进一步分离后进入压缩机压缩温度、压力升高后作为热源进入蒸发器壳侧对原液进行加热,蒸汽释放潜热后变为冷凝水进入冷凝水罐;5、分离器中分离出的原液经循环管进入蒸发器继续蒸发;6、冷凝水罐中的冷凝水一部分经喷水泵进入压缩机对压缩机进行润滑密封和消除过热度,另一部分经冷凝水泵进入预热器对原液预热后排出,进入其它处理系统处理。关键技术或设计特征
该工艺采用板式换热器预热技术,充分利用冷凝水热量,提高进入系统的原液温度。
采用一次蒸发、多次分离技术,去除蒸汽中夹带的液滴,有效保护压缩机,并提高污水净化效率,使出水稳定达标。
采用上位机操作,使操作人员与系统分离,提高了自动控制水平,改善操作人员工作环境。
典型规模
该系统能够达到10t的日蒸发量,吨水能耗50kW˙h。
推广情况
在广东汕头有蒸发量200kg/h的硝酸银处理系统;江苏镇江有处理量10t/d的电镀废液处理系统;河南新乡有处理量1t/h的硫酸锌处理系统。
15、节能型工业高氨氮废水处理技术
适用范围
适用于处理石油、化工、冶金等行业产生的高氨氮废水。
基本原理
当溶液中pH值在10.8~11.5时,溶液中铵离子将转变成游离氨,此时废水中的氨通过蒸汽汽提的方法易于从液相进入气相,进入气相的氨与稀硫酸反应生成硫酸铵,生成的硫酸铵可作为催化剂制备过程中的原料回用,从而达到废水脱氨的目的。
工艺流程
1.将预处理后的氨氮废水与脱氨后的废水经过闪蒸的蒸汽通过文丘里喷射器直接加热后,加入碱液调节pH值后,送入脱氨塔汽提段的顶部,与脱氨塔汽提段底部来的蒸汽进行逆流接触,汽、液两相在塔内的填料层发生传质,废水中的游离氨气进入汽相。
2.脱氨后的废水进行闪蒸降温,闪蒸产生的蒸汽再进入文丘里喷射器和高氨氮废水混合加热预处理的高氨氮废水,实现脱氨前废水和脱氨后废水的热量交换。闪蒸后的脱氨废水温度降至60℃左右排放。
3.脱氨塔顶部出来的含氨蒸汽经过蒸汽循环热泵增压后进入吸收塔进行氨气吸收。吸收塔同样为逆流设计,含氨蒸汽由塔下部进入塔内,循环吸收液经硫酸循环液泵由塔上部进入塔内。在吸收塔的填料层中汽、液相发生传质及酸碱中和反应,且反应为放热反应,所放出热量最终产生部分蒸汽,在脱氨过程中得到充分利用。
4.蒸汽中的氨被硫酸循环吸收液所吸收,重新变得洁净的蒸汽,以及硫酸和氨反应放热产生的蒸汽一道经过蒸汽喷射器,由公用工程来的补充蒸汽引射增压后,送入到汽提脱氨塔循环使用。
5.硫酸循环吸收液携带着中和反应产物硫酸铵进入塔底。
6.当循环液的pH值到达一定条件时,将吸收循环溶液送到分子筛制备单元,作为原料使用。
关键技术或设计特征
将汽提脱氨技术、节能热泵技术、真空闪蒸技术集成创新。
汽提脱氨后废水经过两次减压闪蒸技术,以进一步降低脱氨废水中的氨氮含量。
该项目采用的吸收塔,将汽提后携带有氨氮的蒸汽用稀硫酸吸收,吸收后形成的硫酸铵作为分子筛合成过程中的原料使用,而经过吸收后重新变得洁净的蒸汽通过热泵机组增压后作为汽提蒸汽循环使用,从而大大的降低了蒸汽消耗量,显著地降低了分子筛生产的成本。
典型规模
催化剂长岭分公司建成75t/h高氨氮废水处理工业装置;
催化剂齐鲁分公司建成了40t/h高氨氮废水处理工业装置。
推广情况
该项目技术已在中国石化催化剂长岭分公司和齐鲁分公司、中石油抚顺石化公司、青岛惠城石化科技有限公司推广应用。
16、利用余热资源化处理焦化脱硫废液技术
适用范围
采用氨法湿式氧化脱硫工艺的焦化企业
基本原理
主要是基于脱硫废液中的主要污染物硫氰酸铵等铵盐的热稳定性较差,在425℃前即可全部分解为NH3,H2S、CO2和N2等气体。而焦化企业荒煤气的温度高达750℃左右,同时通过热量衡算表明,焦化企业在炼焦过程中产生的荒煤气从750℃降至500℃的热量足够热解企业产生的全部脱硫废液。因此,脱硫废液以雾状形式进入荒煤气后,在荒煤气的高温作用下即可全部分解,从而实现脱硫废液的资源化处理。
工艺流程
脱硫废液经精细过滤后,进入喷射器,经喷射器喷嘴雾化后的脱硫废液和上升管底部的高温荒煤气(750℃-900℃)接触后,在高温条件下,脱硫废液中的NH4SCN等有害物质分解为NH3,H2S、CO2和N2等气体后随荒煤气一起进入随后的初冷和化产回收系统(焦化企业现有的系统),污染物NH4SCN最终以S和NH3等资源回收。其工艺技术方案如图所示。
关键技术或设计特征
开发了内衬耐火砖高温(800℃~1000℃)打孔技术并研制高温打孔冷却液。
采用具有自清洗功能的过滤装置,使过滤后固体颗粒小于50μm。
建立了喷射器中介质自动切换的自控系统,使脱硫废液的处理过程能够自动运行。
采用耐高温、高压和强腐蚀脱硫废液喷射器,强化脱硫废液热解能力。
开发了防滴漏、自清洗抗积炭的精细雾化喷雾技术,使雾化后雾粒到小于100μm,并能在高温及强腐蚀性的环境下不产生滴漏现象。
典型规模
在屯留县华诚焦化有限公司建立的工业化运行装置,处理规模为4000t/a脱硫废液,并于2014年初实现成功运行,目前运行过程稳定,处理效果良好,达到了预期的所设计的效果。
推广情况
目前正在为山西省焦炭集团有限责任公司益兴焦化厂(规模为100万吨/年)建设12000t/a利用余热资源化处理脱硫废液技术示范工程。
17、高含盐废水综合治理技术
适用范围
石油、天然气、石化、化工、农药等行业产生的高含盐废水的处理及废水浓缩。
基本原理
利用气液平衡和固液密度差分离原理,实现固形物和液相有效分离。
工艺流程
废水经预处理脱除H2S等还原性物质,再经过三相流分离,通过气液分离使冷凝液中Cl-含量降低,冷凝液处理后经吸附去除CODCr,回收利用或达标外排;三相流分离冷凝液的同时,结晶析出氯化钠,通过固体收集器确保产出氯化钠达到精制工业盐优级标准,使废水得到综合治理,达标排放,并回收利用废水中的部分有用资源的目的。 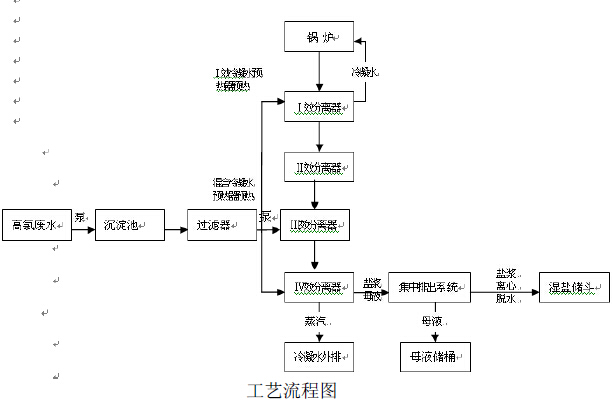
关键技术或设计特征
采用三相流分离技术。
稳定分离出水氯根技术,开发出新型带自动冲洗的气液分离装置,使冷凝液Cl-含量≤10mg/L,达到国家污水综合排放标准(一级)和锅炉用水标准。
盐质洁净技术,开发出新型带浮选装置的固体收集器,增加淘洗功能,达到较高的排放固液比,保持固体排放通畅及浮选产品的纯度及质量要求。
典型规模
1、天然气废水处理能力360m3 /d或11.98万m3 /a;
2、天然气废水处理能力700m3 /d或23.3万m3 /a;
3、天然气废水处理能力1150m3 /d或38.3万m3 /a。
推广情况
中石化川西气田水二期处理装置,设计处理能力700m3/d,2014年9月投产;中国石油安岳气田水处理装置,设计处理能力375m3/d,2014年10月投产;土库曼斯坦气田水处理装置,设计处理能力1150m3/d,预计2016年初投产;中石化元坝气田水处理装置,设计处理能力700m3/d,预计2015年底投产。
18、同轴电絮凝水处理系统
适用范围
适用于有机化工、石油化工、印染、医药、农药等高浓度、毒性大、难生化降解的有机废水处理。
基本原理
采用电化学原理去除废水中的杂质,产生易去除的不溶解于水的氧化物和氢氧化物。在一般情况下,电场作用于电极上,产生离子或释放的电子在进入水体时产生氧化、还原、絮凝、气浮等物理化学反应,反应器本体在不同要求的用途下,配合高频电源还可以发生较强络合反应或螯合反应,使得一些难以去除的物质以络合胶体的形式沉淀出来。对于氯离子,可以跟羟基和其他物质形成卤化复合物絮体。同时,配合高频电源及敏化剂的使用,可以发生诱导催化氧化反应,使氧化、还原反应进行的更彻底。从而可使CODCr、氨氮等除去率可高达90%以上。
工艺流程
含砷废水电絮凝处理的工艺流程为:污水经过格栅去除粗大杂物后进入长廊道式调节沉砂池,调节池后部设集砂斗去除雨水冲刷带来的泥沙。在出水中投加碱液将pH调至8~8.5,经预处理砂滤器去除碱反应产生的悬浮絮体。出水依次泵入四级电絮凝反应器(每级12个反应器)除砷。中间设砷浓度在线监测仪,如砷浓度达标可提前直接排放,反之则进入下一级继续处理。
单反应器处理水量:4.5m3/h
每级反应器砷去除率:≥90%
每级絮凝剂加药量:10~15mg/L
单个过滤器容:过滤面积4.52m2,滤速10m/h。
外形尺寸:φ2.4×6.5m,碳钢防腐
栅渣和沉砂池泥沙采用人工定时清理,堆积自然干化。每一级过滤器分离出的污泥中含有大量的砷,经稠化脱水后送到指定地点集中处理,脱水液送入前段调节池。
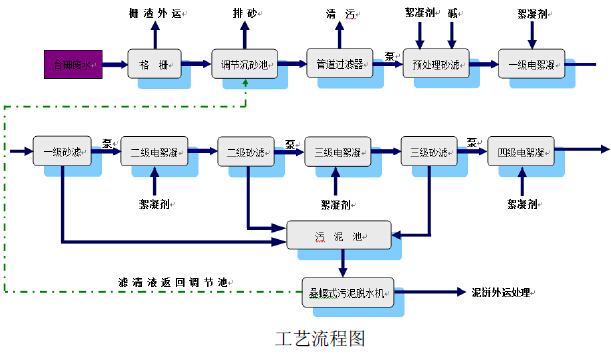
关键技术或设计特征
预处理段由调节池(1000m3)和澄清池组成。调节池内设有液位开关,控制电絮凝处理段的进水泵启停。
处理段由电絮凝装置和砂滤器组成,为四级反应器串联使用。第一级反应器出水悬浮物絮体含量较大,固液分离采用两台过滤器,后面三级反应器出水均采用一台过滤器。五台过滤器出水可直接排放,也可以根据要求串联排放。
整个系统操作均由计算机自动控制。
典型规模
公司承建的“阳宗海流域澄江锦业工贸有限公司含砷废水治理示范项目”,设计规模为1000 m3/d,设计进水砷含量≤100mg/L,出水砷含量≤0.05mg/L,去除率达到99%,水质稳定达到地表水Ⅲ类标准。
推广情况
已应用于个旧乘风有色金属股份有限公司、个旧双龙贵金属实业有限公司、个旧金鹰工贸有限公司、石药集团中国内蒙古中润制药厂污水处理等项目重金属废水处理的项目中。
19、稀土磁盘分离净化废水技术
适用范围
适用于轧钢、连铸浊环水净化,转炉污泥富集金属铁、铁矿尾矿洗选,金属研磨废液净化等。
基本原理
在冶金过程中产生的废水多含有铁磁性及顺磁性物质,利用稀土磁盘的高强磁场将废水中的磁性、弱磁性的悬浮物打捞分离出来,从而达到水质净化和磁性物回收的目的。
工艺流程
1.当流体流经磁盘之间的流道时,流体中所含的磁性悬浮絮团,受到强磁场力的作用,吸附在磁盘上,逐渐从流体中分离出来;
2.磁盘通过旋转让悬浮物脱去大部份水份,运转到刮渣条时,由刮渣轮刮入“螺旋输送机”,渣被输入渣池;
3.卸渣后磁盘重新转入流体,达到废水净化、悬浮物回收、循环水回用的目的。
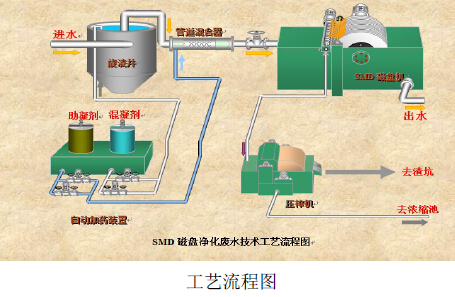
关键技术或设计特征
混絮凝技术:药剂复合后一次投加,使用单台投药机,投资省。
NdFeB防腐蚀技术:对NdFeB材料磁环的防腐蚀、防氧化,实现了低成本、高效果的NdFeB防腐蚀、防氧化处理。
磁盘分离技术:利用稀土磁盘的高强磁场将废水中的磁性、弱磁性的悬浮物打捞分离出来。
推广情况
该技术已在首钢、柳钢、攀钢等大型钢铁企业应用。
20、印染废水治理及污泥减量新技术
适用范围
染整行业印染废水的达标处理及污泥减量。
基本原理
该技术采用基于新材料的模块反应器工艺,先经基于HY剂的预处理反应器充分改变水中有机物结构,断链开环,提高B/C比;然后通过基于CSE剂的反应器氧化降解去除水中残余色度、部分CODCr和磷,色度≤8,污泥量减量85%以上;再经A/O工艺,去除大部分CODCr、氨氮和总氮;最后经基于高性能改性PP滤材的高密度生物膜反应器(HBF)高效脱氮,出水无需沉淀即稳定满足《太湖地区城镇污水处理厂主要水污染物排放限值》纺织染整工业的标准要求。将经带式压滤机压滤后泥饼投入基于CSE-G剂的污泥循环再利用反应器中改质,被有机质包裹的无机铁泥成分活性提高,100%循环再利用,少量有机泥车间焚烧。
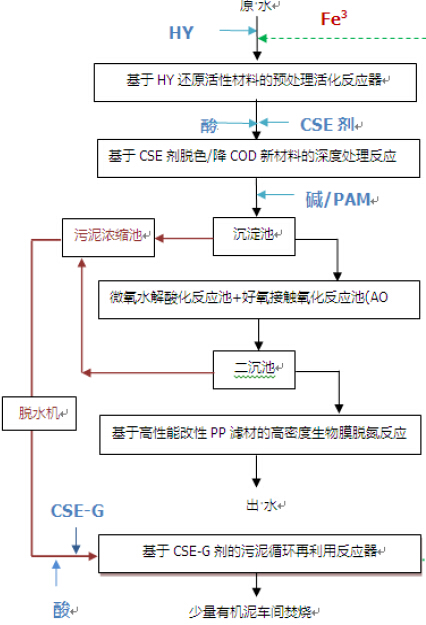
工艺流程
1.印染废水泵入基于HY剂活性材料的预处理活化反应器中,在HY剂与回流的改质Fe3+协同作用下搅拌反应2h,充分改变废水中有机物结构,发生断链开环等预处理,提高B/C值;
2.经步骤一处理出水进入基于CSE剂脱色/降CODCr新材料的深度处理反应器中发生高级氧化反应,在酸性条件下将水中残存的色度进行高效去除,解决原有工艺脱色污泥量大问题并去除部分CODCr和磷;系统出水经中和絮凝沉淀后进入AO生化系统进行生物处理,污泥直接排入污泥浓缩池;
3.AO单元采用接触氧化工艺,主要去除废水中大部分CODCr、氨氮、总氮等,再经沉淀,分离出的污泥进入污泥浓缩池,此时出水暂不能达标;
4.上述出水利用基于高性能改性PP滤材的高密度生物膜脱氮反应器(HBF)进行高效处理,无需沉淀池其最终出水稳定满足《太湖地区城镇污水处理厂主要水污染物排放限值》纺织染整工业CODCr≤ 50mg/L、氨氮≤5mg/L、总氮≤15mg/L、总磷≤0.5mg/L的标准要求。出水稳定达标,污泥减量85%以上。
5.污泥回用即浓缩池中的污泥经带式压滤机压滤后泥饼投入基于CSE-G剂的脱色污泥循环再利用反应器中进行改质,基于氧化剂及β-葡聚糖酶协同作用,被有机质包裹的无机铁泥成分活性提高,100%满足系统循环再利用要求,其余的有机污泥(夹带少量的无机铁泥)直接运到车间锅炉焚烧。
工艺流程图
关键技术或设计特征
基于HY剂活性材料的预处理活化反应器技术
基于CSE剂脱色/降CODCr新材料的深度处理反应器技术
基于高性能改性PP滤材的高密度生物膜脱氮反应器(HBF)技术
基于CSE-G剂的污泥循环再利用反应器技术
典型规模
句容市工艺织造厂处理规模:1000m织造厂。
推广情况
该技术涉及的各单元技术推广应用情况具体如下:
1、基于HY剂活性材料的预处理活化反应器主要应用于句容市织造厂、民达污水处理厂等多家单位;
2、基于CSE剂脱色/降CODCr新材料的深度处理反应器主要应用于上海吉田拉链有限公司、句容市织造厂等5家单位;
3、基于高性能改性PP滤材的高密度生物膜脱氮反应器(HBF)主要用于句容市工艺织造厂;
4、印染废水深度处理工艺智能化控制系统研制主要应用于上海吉田拉链有限公司、句容市工艺织造厂、民达污水处理厂等单位。